Preventive maintenance skills learning in the technology laboratory
- Diego Saavedra Rojas
- Jun 8, 2019
- 7 min read
Updated: Jun 10, 2019
STEM education methods in universities and community colleges could include techniques that satisfy labor market actual and future requirements through practice of preventive maintenance techniques.
Keywords: STEM education, Technology Education, Liability, Reliability, Preventive Maintenance, Skills.

Context of Preventive Maintenance in current times.
Contemporary and prospective professionals comprehend the generational change in which information, markets, and capital move rapidly and cheaply. Engineering & Technology Education laboratories, Maker-spaces, and Science Technology Education & Mathematics (STEM) instruction workrooms provide a hands-on, self-directed, collaborative environment. These spaces emulate the setting, tools, and machinery requested in their future duties inside the workplace. It also legally implies acknowledgment of substantial matters such as safety and maintenance. On the other side, preventive maintenance comprises an essential component inside any industrial company that engineers, supervisors, operators, trainees, and interns must domain. Its systematic application ensures high performance, reliability, and safety in every productive-operational environment. Actual trends require professionals more than ever being proficient in employing integrative technologies, reliable proceeding, and modern techniques in order to succeed among their competitors. Some of these tools request investing productive time inside lessons, lectures, and orientations that hinder the purpose of having a self-learning and learn-by-doing environment. Even though it demands resources employment, a robust Preventive Maintenance system at Engineering & Technology Education Laboratories based on continuous improvement enhances safety, costs reduction, and fosters students' skills required in the future the labor market.
Repairing a system is much more expensive than replacing it after reparations, literature suggests.
Preventive Maintenance (PM) is a maintenance task executed on a programmed foundation in planned intervals, all based on suggestions from manufacturers and previous know-how about the equipment (Ben-Daya, Duffuaa, & Raouf, 2000). It entails replacement, amends or both. There are two statements recommended to follow by Ben-Daya et al. (2000), repair a system is more expensive than replacing it after an extensive amount of reparation. And the reparation cost of a failed system is much more than fixing an operative structure. PM role in ensuring hazards sources are controlled is crucial. Records are an excellent input for identifying jobs to analyze and review in order to ensure safety (Roughton & Crutchfield, 2016). Deficient housekeeping and maintenance labors are immediate indicators that the quality of the workplace is insufficient which implies the significant presence of hazards and risks. Lean Maintenance is a recent term concentrated on Total productive Maintenance (TPM). TPM comprises elimination of hazards and accidents, defects and breakdowns. It is focused on team management, pro-activity, efficiency and quality (Kister & Hawkins, 2006). This concept equally involves the idea of Lean thinking which seeks to eliminate waste, focus on customers and generate quality.
Preventive Maintenance Drives Safety inside a Self-learning Environment
A well-developed preventive maintenance system at Engineering and Technology Education Laboratories based on continuous improvement enhances safety. It is inherent to link safety with Preventive Maintenance in modern times. According to Toglia (2009), Career Technical Education (CTE) facilities must develop a PM plan for eliminating and controlling hazards, in order to institutions and instructors be legally liable. In the same way, students must evidence training in how to handle hazardous as well as know how to deal with potential risks. By doing so, Preventive Maintenance would enhance the meeting of these requests and also ensure equipment reliability, which reduces risks and provides operational documentation. This last statement relies on the fact that records and information related to PM plans provide background and evidence about liability to institutions while performing activities with laboratory equipment.
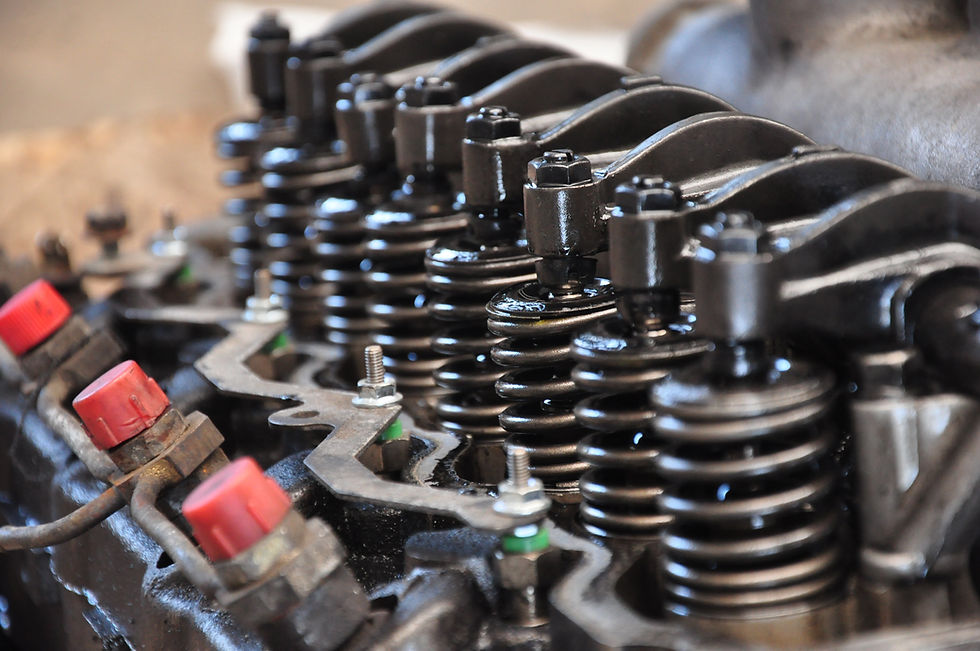
Maintenance systems indeed impact in costs reduction
A well-conducted PM plan focused on students reduces overall expenses. Based on the foundations of Lean practices and Continuous Improvement philosophy, performing preventive maintenance rise economical savings since it prevents equipment failures. Kister and Hawkins (2006) suggested that in the manufacturing industry, expenses related to maintenance comprises a range between 14% and 25% of their total operational costs. Making the best use of repairs ensures competitiveness enhancement and waste reduction.
PM reduces chances failure, increments reliability in equipment, ensures the right operation, and enlarges the life of the articles. Failures are translated in expenses on breakdowns, replacements, inventory, and reparations. Students learn responsibility about tools and machines employment while performing maintenance tasks and managing the PM plan. They embrace techniques to complement their essential knowledge. Consequently, warranty policies in machinery request as obligatory insurance to keep records and spreadsheets with all the activities typically done to the machine. Then, PM plans ensure the capacity of having complete suppliers support if it is required. Students with a focus on costs savings, resources optimization, regardless of their major and final minors, are highly valued and requested in successful companies. In another words, it reflects how well trained is the prospective professional. Additionally, it is merely valuable to consider that risk management and maintenance plans indeed ensure financial stability by reducing expenses related to lawful concerns, prevent lawsuits, insurance, guarantees, accidents, to name a few.
What the future demands of skills looks like
Ultimately, a well-developed Preventive Maintenance system at Tech Education facilities enhances students skills required the current and future labor market. Walls and Stimer (2018) recommended developing a student-focused but a teacher supervised Maintenance Plan with both preventive and routine tasks. Skills developed inside the education laboratory inspire in students abilities of planning, documenting, and records handling. Plus the technical and elementary knowledge about specific reparation procedures, machinery, and tools. Implicitly, students are going to learn other disciplines, distinct methodologies, and techniques for machinery management. According to Storm (1993), the results of involving students in maintenance are highly recognized for occupational instructors. In fact, the evidence provided Jim et al. (2016) suggest attractive findings. They conducted a research among Manufacturing and Technology organizations inside the United States. Their conclusions refer that human resource availability oriented to preventive maintenance systems represent the second barrier that hinders companies to employ PM plans. The authors also stated the trends were running in the way of including preventive employees, in terms of maintenance, in both large and medium-sized enterprises. Love (2014) highlighted that technological literacy and next science generation standards are both keys requested skills when designing and engineering solutions (As quoted in Walls & Stimer, 2018).
Skeptical perspectives can also provide valuable input
Critiques about Preventive Maintenance inside the learning place might indicate that this process represents expenses, students should not be involved with tasks responsible by academic institutions. As the literature review suggests, maintenance plans demands time in planning, managing, supervising, and performing the tasks. Valuable time that could be better used for deep training and projects assignments to students. These same constraints in resources utilization might hinder the purpose of teaching at Technology Laboratories. Machinery educational spaces purpose is generating a self-directed and creative environment that enlarges students' engagement with processing and manufacturing, for example. These arguments are indeed valuable and represent close situations to reality. However, as the sources of information suggest, the earnings obtained from PM plans are invaluable since represents a philosophy of ensuring superior efficiency in both operational and academic aspects. As Walls & Strimel (2018) suggested, the fact that students can sustain themselves involved in maintenance and safety inside the laboratory benefits instructors to detect defective machinery. It also sets good practices for their future. The challenge is to properly meet Liability, Safety, and Instruction in benefit of both students and academic institutions.

Final considerations
In summary, it was shown three key beneficial outcomes of applying preventive maintenance plans while teaching future Engineering or Technology field related professionals. Beforehand, it enhances safety since the activities performed are going to ensure the reliability of equipment. Moreover it will provide evidence for ensuring administrative liability. Secondly, PM plans can circumstantially lessen costs since it would meaningfully reduce failing probabilities, and time and resources efficiency as well. And third, PM Plans performed by scholars and managed by instructors are going to provide valuable experiences to enhance skills in students. Skills highly requested for nowadays employers. The opposing perspective and critiques might point out that PM activities should not comprise the student's responsibility and deviate the purpose of laboratories in superior education. The evidence, however; suggest enormous gains of applying PM Plans and getting learners involved to become assets in knowledge and skills for their professions. Limitations to this research are related to the resources availability and purpose of the education laboratory, in addition to the technical or advanced level of the courses for them. Some workplaces might not request extensive aid from software for PM. The recommendations for both institutions and instructors are to innovate strategies for enhancing student's abilities. In addition to fulfill curricular requests being accountable and legally correct. Continuous feedback from customers, students, alumni, and prospective employers is immensely valuable to process, analyze, and consider in order to integrate demands and perceptions of the outcomes of hands-on education. Lean thinking and several modern trends oriented to operational excellence, revolutionary technologies, and profitability must be researched and incorporated inside programs. Regardless of the nature of the institution and their purpose, sooner or later paper records, checklists, spreadsheets, or advanced maintenance systems are going to be mandatory procedures to generate earnings to both students and universities.
References
Ben-Daya, D., Raouf, B., M., Duffuaa, S., & Raouf, A. (2000). Maintenance, Modeling, and
Optimization. Boston: Kluwer Academic.
Graves, C., Graves, A., & Rendina, D. L. (2017). Challenge-based Learning in the School
Library Makerspace. ABC-CLIO.
Hatch, M. (2014). The Maker Movement Manifesto: Rules for Innovation in the New World of
Crafters, Hackers, and Tinkerers. New York: McGraw-Hill Education.
Kister, T., & Hawkins, B. (2006). Maintenance Planning and Scheduling Handbook: Streamline Your Organization For a Lean Environment. Amsterdam: Elsevier Butterworth-Heinemann.
Roughton, J., & Crutchfield, N. (2016). Job Hazard Analysis: A Guide for Voluntary
Compliance and Beyond. Waltham, MA: Elsevier Inc Butterworth-Heinemann.
Storm, G. (1993). Managing the Occupational Education Laboratory. Ann Arbor, MI: Prakken
Publications, Inc.
Toglia, T. (2009). Keeping It Safe: Safety and Liability Advice for CTE Programs. Tech
Directions, 68(6), 17-21.
Walls, W. H., & Strimel, G. J. (2018). A Well-Maintained Lab Is a Safer Lab. Safety Spotlight.
Technology and Engineering Teacher, 77(6), 16-19.
Comentarios